Posted by
MarkR on
URL: http://riverswest-forums.266.s1.nabble.com/Point-Comfort-23-tp527p574.html
It was time to glass the hull. Luckily I was able to recruit Randy T. and Charlie E. to assist and we got a stretch of four or five days of projected 50 degree plus weather in the same time window. Prior to applying the glass, the whole boat was sanded to 80 grit. The Rotex and I became really good friends!
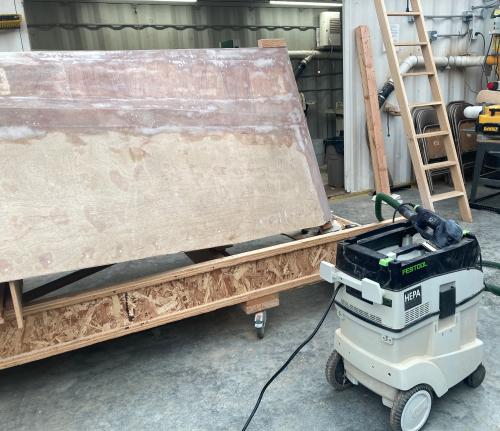
We decided on Saturday that we would do half of the boat on Monday, then the other half on Wednesday. That gave us time to prime on Sunday and Tuesday. We were concerned that trying to do it all in one shot was going to exhaust us. That would lead to mistakes. Better to be safe.
On Sunday, I went to the shop, wiped the hull down dry, then wiped the aft 11' or so down with towels and denatured alcohol until the towels came up clean. Once the hull was as clean as I could make it, straight epoxy was applied. We are using Silvertip epoxy from System Three. It doesn't blush, wets out well with our 10 oz. cloth and can be re-coated the next day for a chemical bond. All good attributes. The transom had been glassed prior to this work.
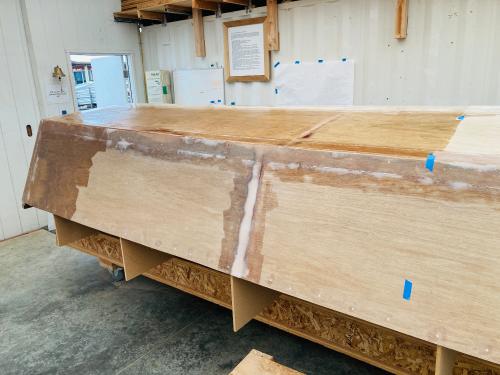
Monday morning I was able to sand the primed epoxy, using the Festool HEPA dust extractor and a mask for protection from the green epoxy dust. Then the sanded hull was washed down with towels and denatured alcohol. It's amazing how much dust is removed with the combination of the Festool sander and extractor.
When Randy came in, we draped and cut the cloth to get ready for Charlie who had volunteered to be our mixer. Then we precut and numbered the peel-ply. At that point, the cloth was thoroughly saturated with epoxy.
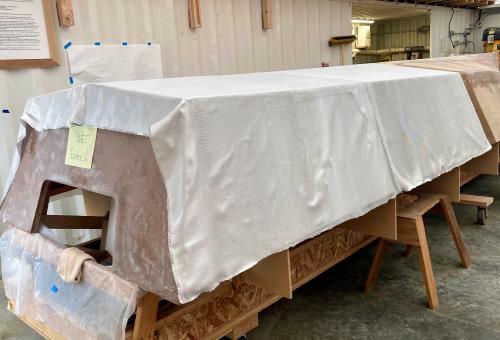
The glass was recoated with epoxy and then we applied the peel-ply, squeegeed it as flat as we could get it, hitting it with the roller when needed. This method makes a thin, strong and smooth lamination. It is a process that Randy has used successfully on several boats and so his help was critical to success.
On Tuesday, the peel ply was pulled and the edges of the glass cloth were trimmed with a box knife.
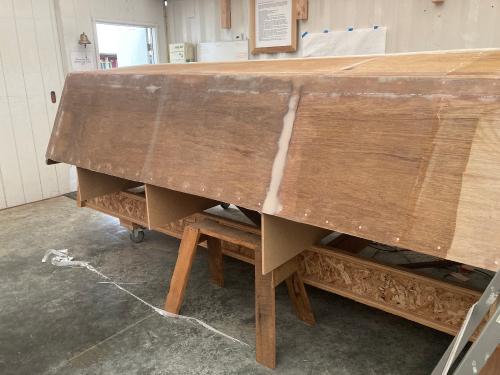
Then, it was on to wiping down the forward end of the hull, sanding and priming with straight epoxy.
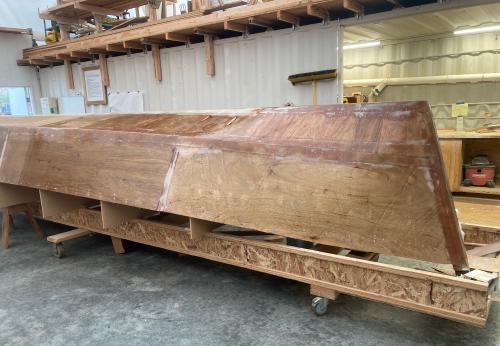
Wednesday the process was repeated on the forward section of the hull. Charlie, our mixmaster was constantly busy both days. I owe him big!
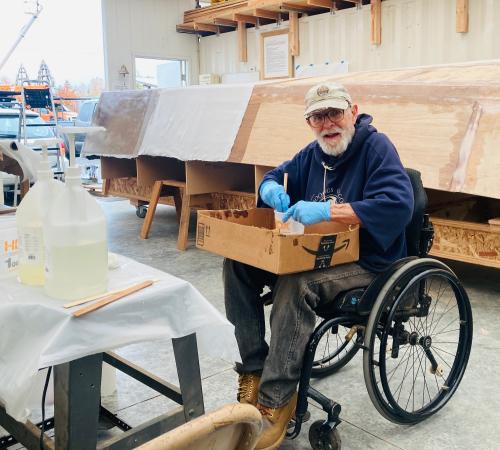
The wetting out process is interesting on this heavier glass. With lightweight glass, the cloth turns transparent very quickly. On the heavier glass it takes much longer. Slow hardener was a must even at the 55 degrees or so in the shop.
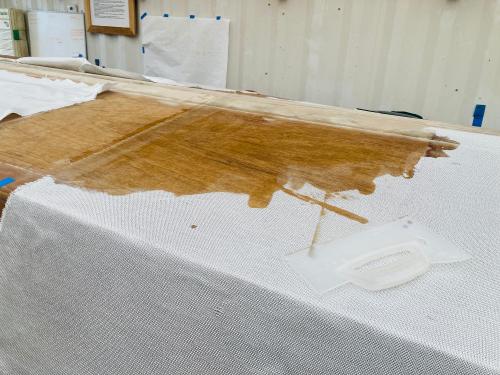
All of the peel-ply is precut to fit, so numbering the panels is important so you know that they are in the right place.
Here the peel-ply is in place on the forward end of the boat.
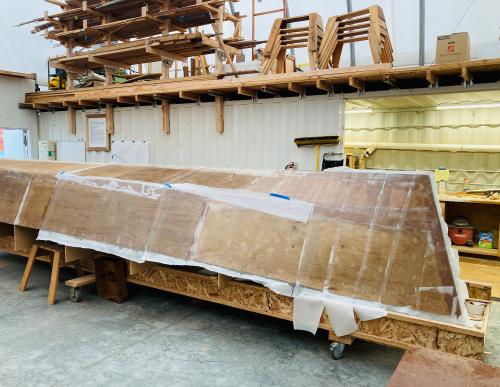
The next day, I returned to the shop to rip the peel-ply and trim the edges. A tribute as to how well this peel-ply lamination technique works is that on this boat we used about 3 gallons of epoxy to apply almost 20 yards of 60", 10 oz cloth.
The job looks great! Many thanks to Randy & Charlie! It couldn't have happened without you two!